Brushed DC Motors Manufacturer
Brushed DC motors offer advantages like cost-effectiveness, reliability and suitability for extreme operating environments. One tremendous benefit they provide is their high ratio of torque-to-inertia. This makes many brushed DC motors well-suited to applications requiring high levels of torque at low speeds. SherryMotor Drive Systems offers a multitude of high-quality and dependable brushed DC motors that suit a variety of applications.
SherryMotor has been manufacturing high-quality and cost-effective electric motors and drives for over a century through some of its trusted brands. The Nidec Drive Systems brands that offer reliable brushed DC motors include Advanced Motors and Drives, Imperial Electric and Scott DC Power Products. If you think one of the products listed below can meet your specifications, please contact us today.
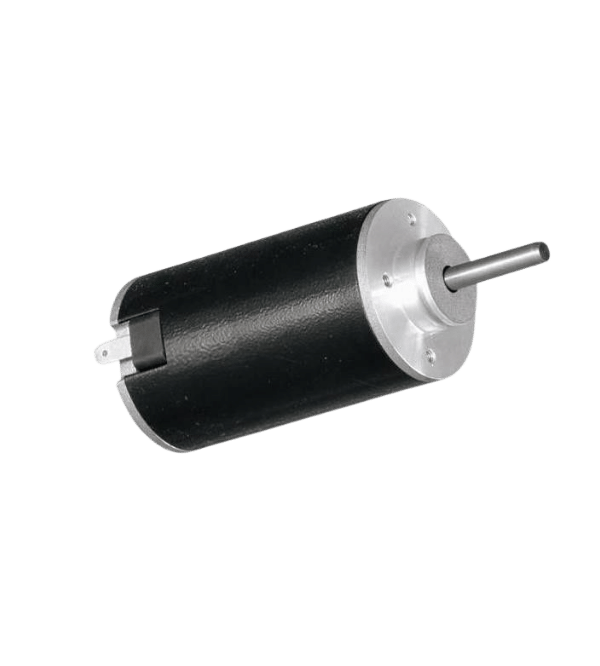
What Is A Brushed Motor?
A brushed DC electric motor is an internally commutated electric motor designed to be run from a direct current power source and utilizing an electric brush for contact.
When electricity is applied to the electromagnet in the armature, a magnetic field is created that attracts and repels the magnets in the stator. The armature rotates in a 180-degree circle. To maintain the electromagnet spinning, the poles must be swapped. The brushes are in charge of polarity shifts. They make contact with the armature’s two rotating electrodes. The magnetic polarity of the electromagnet is reversed as it rotates.
By adjusting the operating voltage or the intensity of the magnetic field, the speed and torque may be adjusted to give a constant speed or a speed that is inversely proportional to the mechanical load.
Advantages of Brushed DC Motor
- Low cost of construction.
- Simple and inexpensive controller.
- No controller is required for fixed speeds.
- The ideal for the extreme environment due to the lack of electronics.
- Two-wire control.
- Rebuild new brush for extended life.
How we ensure a profitable business partnership
Professionally Trained Engineering & Manufacturing Team
- Producing custom-made, DC motors is a complex process.
- Even before the raw materials are trucked to the manufacturing plant and brought to the production line, both the client and electric motor manufacturer have started to solidify their working relationship by laying the ground work that’s required prior to the commencement of production.
- Successful working relationships require trained professionals, including engineering, manufacturing, supply chain, logistics, quality control, among others, to create not only the motor design and prototypes, but also the manufacturing processes and delivery channels.
- Sherrymotors has built a design and manufacturing team of highly trained and customer-focused professionals.
- It leverages both the technical expertise and customer service skills of its staff to ensure production goals occur within budget.
Comprehensive Manufacturing Facilities
- Manufacturing any product requires both the equipment and facilities to handle projected production volume, capacity or throughput.
- Beyond capacity considerations, what’s key for a custom electric motors manufacturer is to have all the machinery, equipment and testing capabilities in house and on-site so it can produce motors from start to finish in a timely fashion.
- Sherrymotors has built a state-of-the-art comprehensive production facility that’s fully equipped to manufacture even high volume runs.
- It’s onsite process equipment includes, CNC machining, shaft splining, automated magnetizing, heat treating, epoxy coating insulation, automated coiling, winding, commutator slotting and balancing, varnishing and welding/painting/special fabrication.
- It also has a testing laboratory, which includes a 30 HP dynamometer and 500 Amp testing capability, to conduct both standard and special tests.
Standardized Work Processes Verified by Quality Control Systems
- One of the motivations for using a custom motor manufacturer is the belief that a specialist can manufacture a motor, quicker, less expensively and with a greater level of quality. It is the ability to manufacture a quality product that reaps both cost and time benefits.
- To obtain a high level of quality, a successful DC motor manufacturer should implement standardized work processes to enhance consistency and reliability. The motors should be tested throughout the production chain to verify this quality.
- Sherrymotors understands the vital importance of manufacturing process control to produce consistent and reliable product.
- Sherrymotors has invested in ISO-9001: 2008 registration and implemented Lean Six Sigma initiatives. All of its machining operations undergo first piece inspections and all of its motors go through end-of-line testing.
- Sherrymotors uses documented manufacturing procedures and its production work-stations are linked to the engineering department to ensure all parts are manufactured to the latest revisions.
Brushed DC Motor List
Key features that set Sherrymotors’ electronically commutated EC motors apart are their excellent torque performance, high power, extremely wide speed range, and unrivaled service life. The outstanding controllability of the motors permits the creation of high-precision positioning drives.
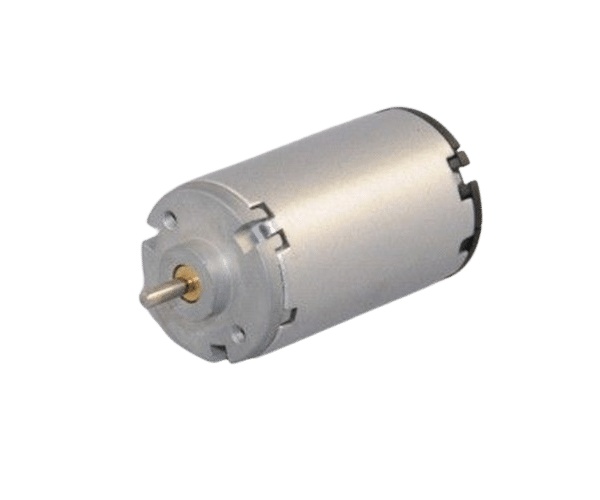
Micro Brushed DC Motor 01343
For product details & specifications:
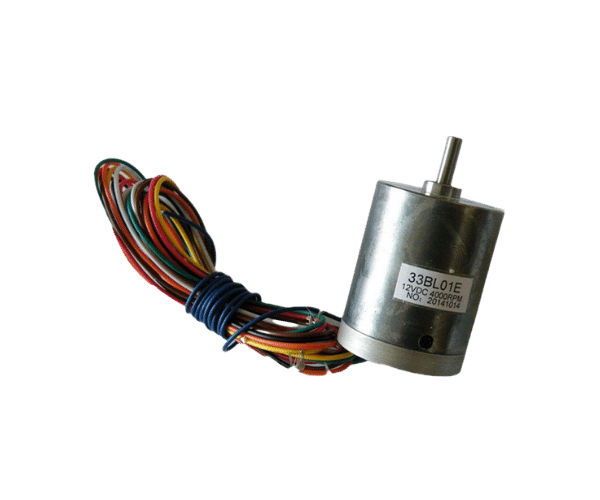
brushless dc motor 33BL
For product details & specifications:
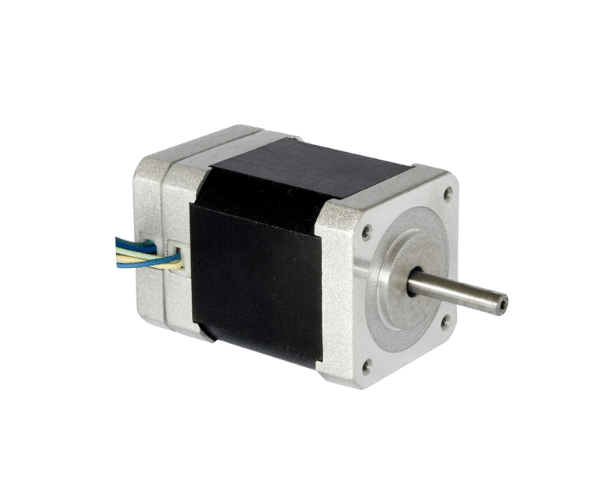
brushless dc motor 42BLF
For product details & specifications:

brushless dc motor 42BLFX
For product details & specifications:
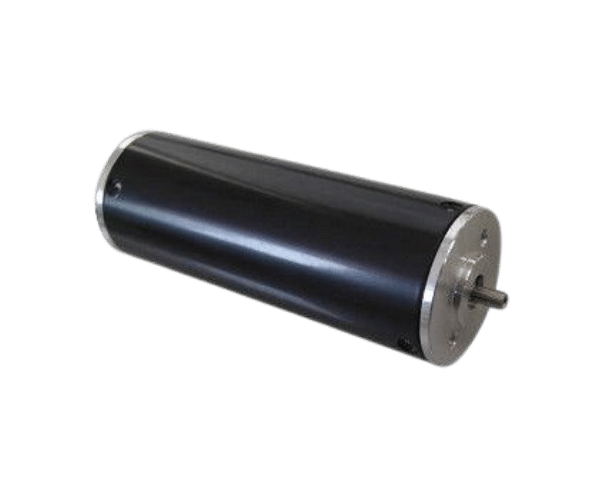
Brushless dc motor 28BL
For product details & specifications:
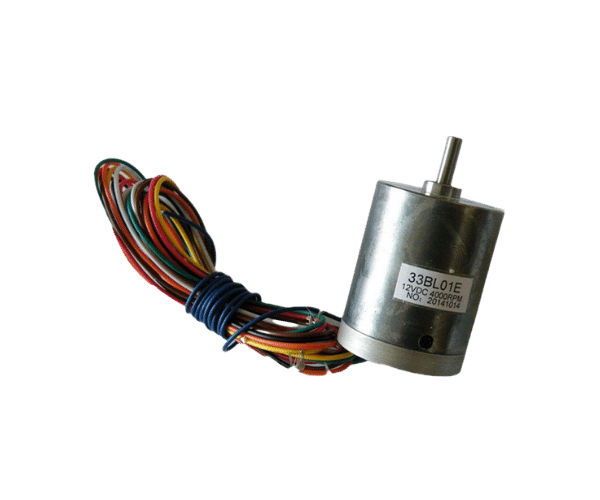
brushless dc motor 33BL
For product details & specifications:
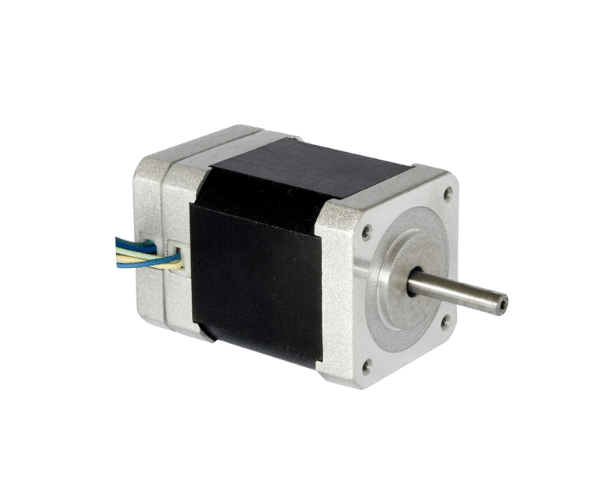
brushless dc motor 42BLF
For product details & specifications:

brushless dc motor 42BLFX
For product details & specifications:
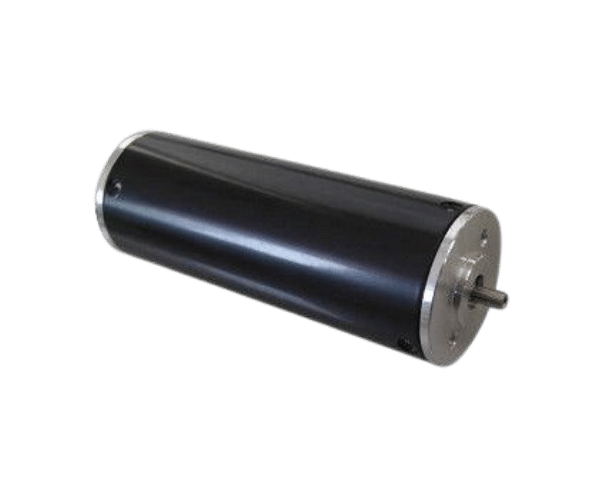
Brushless dc motor 28BL
For product details & specifications:
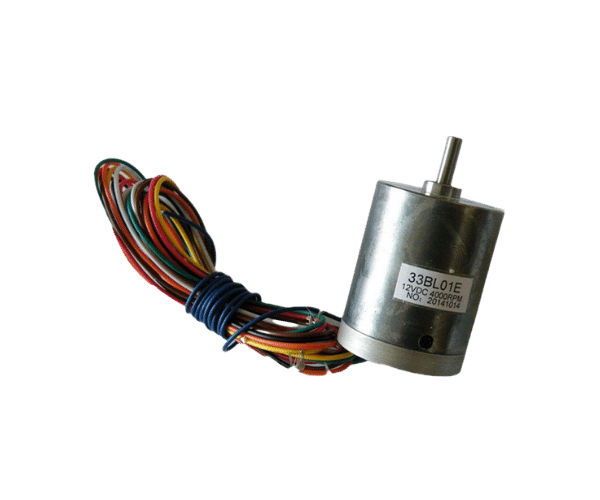
brushless dc motor 33BL
For product details & specifications:
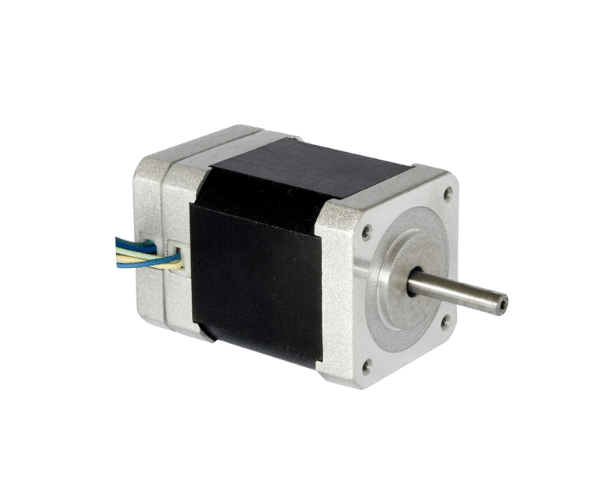
brushless dc motor 42BLF
For product details & specifications:

brushless dc motor 42BLFX
For product details & specifications:
Applications of Brushed DC Motor
Brushless motors fulfill many functions originally performed by brushed DC motors, but cost and control complexity prevents brushless motors from replacing brushed motors completely in the lowest-cost areas. Nevertheless, brushless motors have come to dominate many applications, particularly devices such as computer hard drives and CD/DVD players. Small cooling fans in electronic equipment are powered exclusively by brushless motors. They can be found in cordless power tools where the increased efficiency of the motor leads to longer periods of use before the battery needs to be charged. Low speed, low power brushless motors are used in direct-drive turntables for gramophone records.
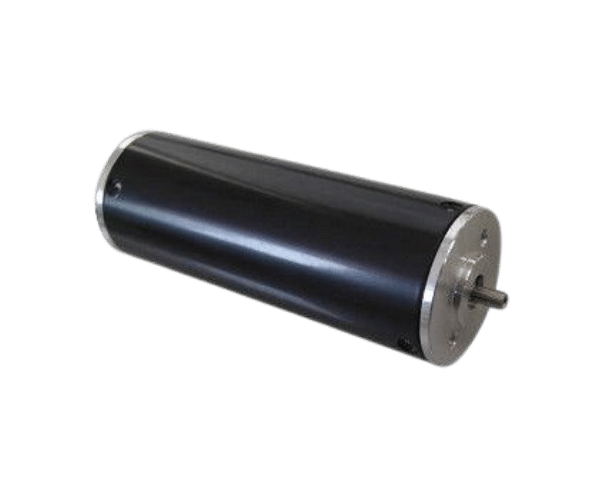
household appliances
For product details & specifications:
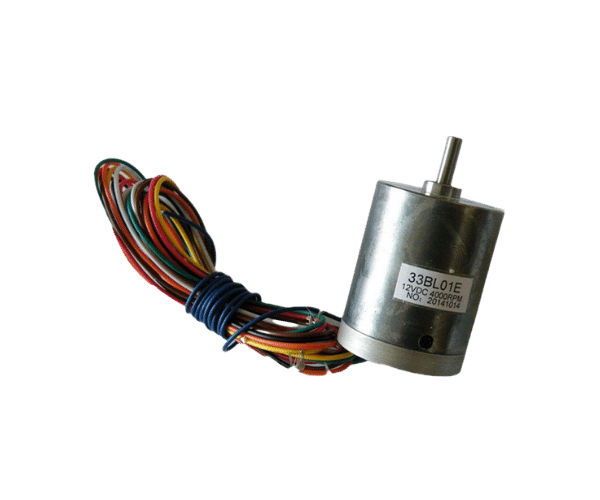
automobiles
For product details & specifications:
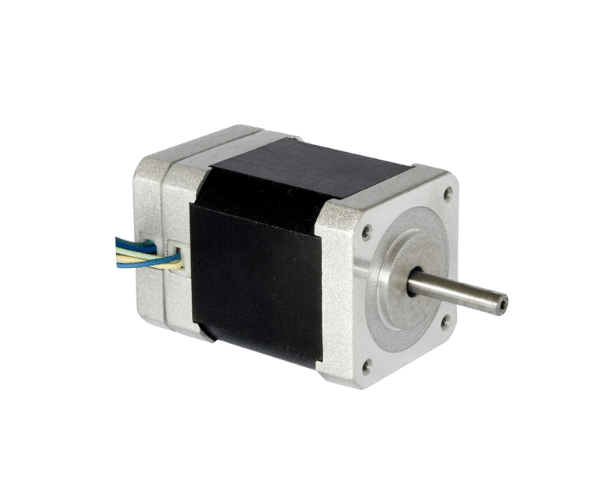
paper machines
For product details & specifications:
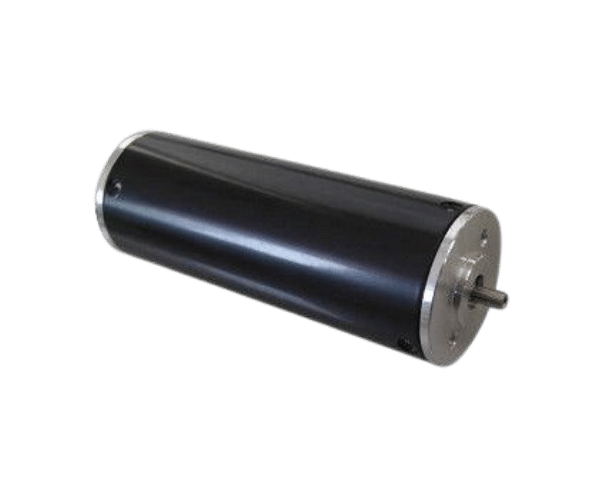
cranes
For product details & specifications:
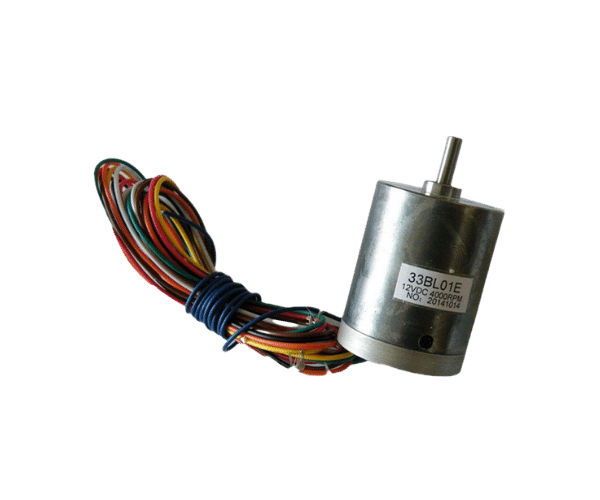
electrical propulsion
For product details & specifications:
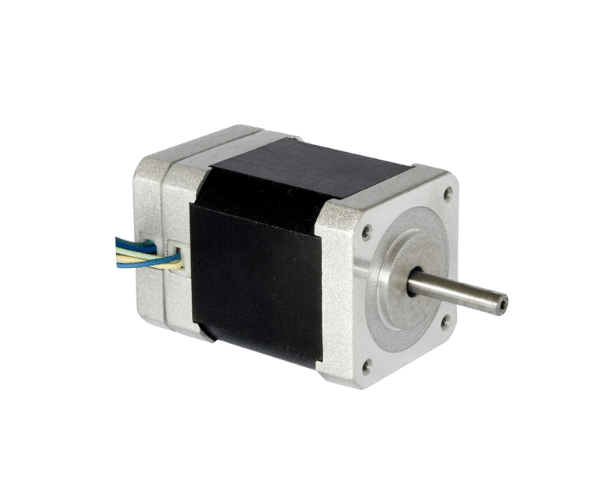
power tools
For product details & specifications:
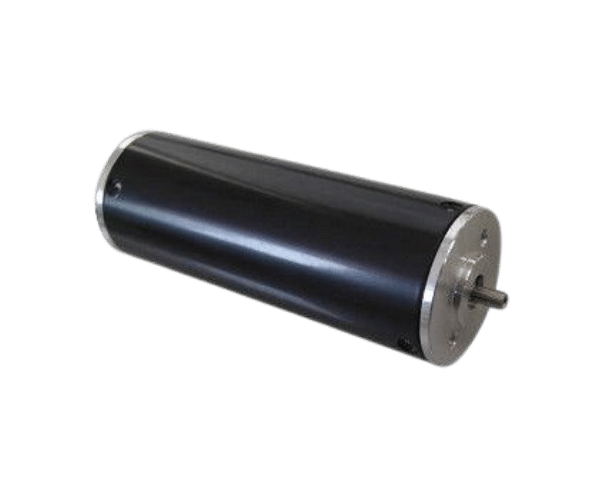
sewing machines
For product details & specifications:
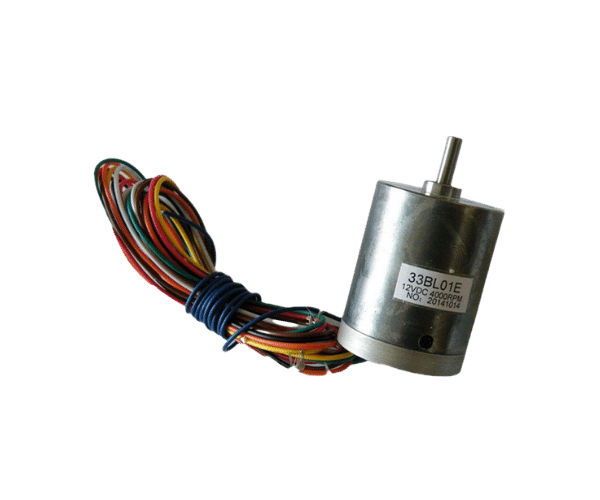
steel rolling mills
For product details & specifications:
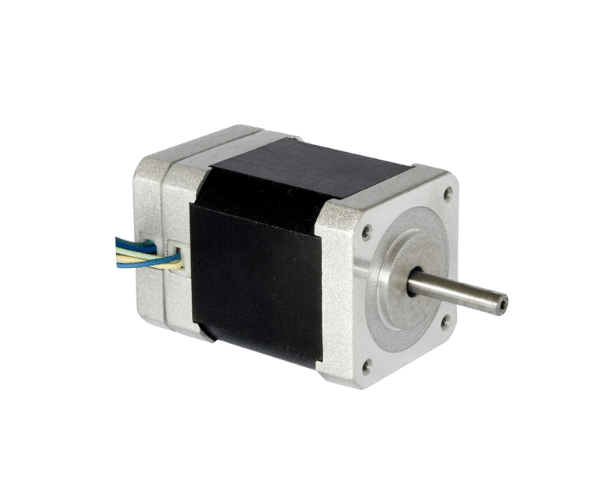
Toys
For product details & specifications:
How to choose Brushed DC Motors?
Brushed DC motors are probably the most common type of motor there is. These motors can be found in everything from hand-held fans and cordless drills, to cell phone buzzers and steel mills. These motors are used to power cars and trains, and not just the toy ones!
Factors to Consider When Buying a Brushed DC Motor
01 Motor diameter
Sizing a brush DC motor to a specific application begins with matching the motor’s diameter to the available space. In general, larger frame size motors deliver more torque. Motor diameter ranges from 8 mm to 35 mm.
02 Length
Various lengths are available, ranging from 16.6 mm to 67.2 mm, to best fit the application package requirements.
03 Commutation type
Precious metal brushes are well adapted to low current density applications, providing low friction and high efficiency, whereas high continuous or peak current applications will require graphite-copper brushes.
04 Bearing type
Several bearing combinations have been designed, from simple sleeve bearing construction to preloaded ball bearings systems for high axial or radial load applications.
05 Magnet and commutation type
Adapt your motor selection to the power and current needs of your application: NdFeB magnets provide higher output torque than Alnico, at a higher cost. The commutation system (type and size of the commutators) is also reflected in this coding.
06 Winding
Various winding options are proposed to best match with the application requirements – voltage, resistance and torque constant are the basic parameters for selection.
07 Execution code
Used to specify standard and customizations.
F.A.Q.
Supporting Subheading
A brushless motor has the advantage of fewer components that can wear down but a brushed motor is more budget-friendly. If you need to pick between the two you must take all factors into consideration and you’ll learn more about it here.
But these aren’t the only motors you’ll find these days. Thanks to technological developments over the years many other devices have come onto the market. One is called a coreless motor.
Ready to get started?
Contact us with your information. Our team will provide you with a customized quote.